Details, timber and DfMA: three strictly related words
This article can be seen as the second part of the article about Digital Model we wrote.
How many times have you seen or heard of a project slowing down or even stopping because of a design error, a miscalculation, or even, worst case, the lack of materials, equipment or drawings on the construction site? Most of the time, all the errors in logistics, design, and production are strictly related to the not sufficient attention to details.
Details, no matter the size, complexity, and location of the project, play a crucial role in determining the correct outcome of the building process and, finally, the whole structure. The deep study of details, while designing, is the basis of DfMA. This approach, which we adopted from day one and still use, permits us to study every single aspect and construction detail in each project no matter how ambitious is. At Ergodomus we came up with the acronym WYDWYG which stands for “What you Draw is What you Get” and perfectly summarizes DfMA principles:
- The ability to virtually design and draw the entire structure in all its aspects, characteristics and small details;
- Deliver an elaborate but extremely clear digital model to the manufacturers making the transition from the design phase to the production phase as smooth and rapid as possible. This phase is crucially important since its success and, consequently, the success of the whole project depends on the correctness of the previously produced designs as they will be imported into the CNC machine;
- The certainty that on the construction site everything will arrive on time, perfectly produced and ready to be assembled/built
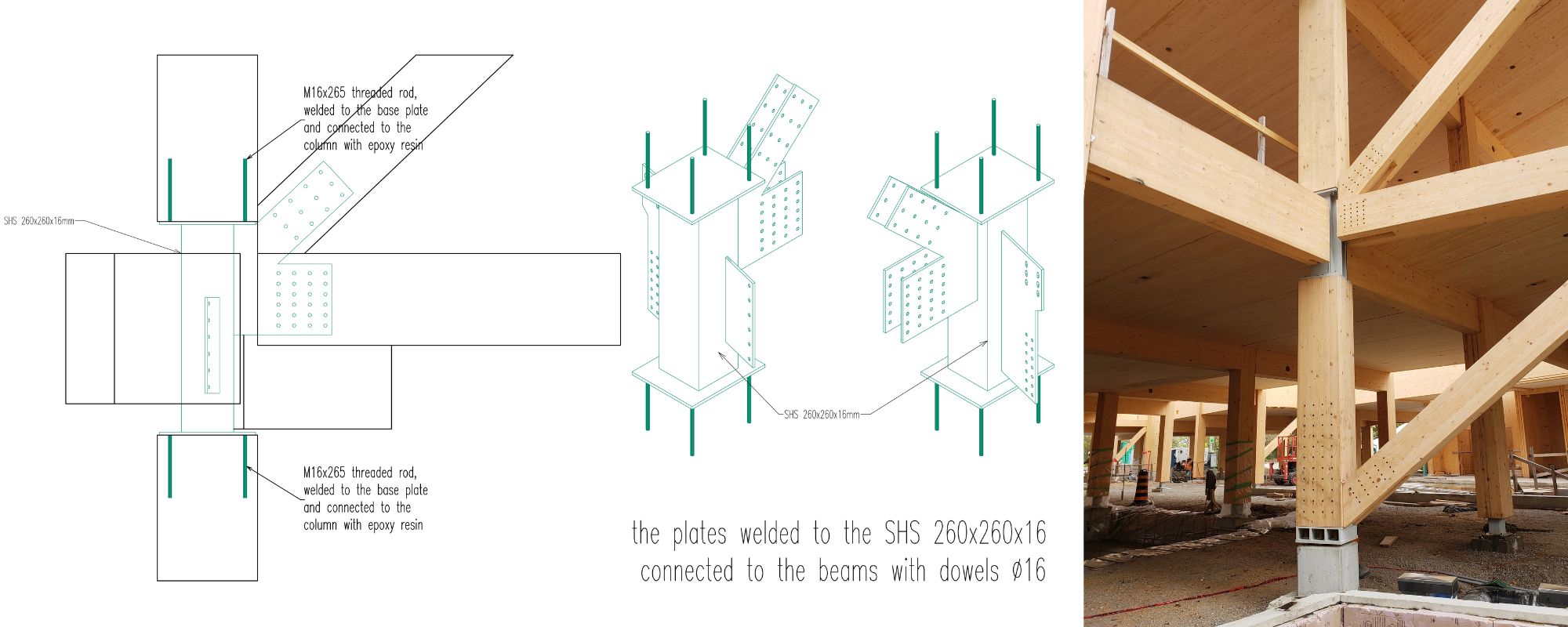
DfMA ensures several benefits like speeding up delivery, reducing labor costs, eliminating unnecessary waste, and improving quality. These are just a few advantages offered but they all depend, as mentioned at the beginning on the quantity and quality of details elaborated during the structural design development and shared with the actors involved.
Having all the details and the project information in a single digital file available to all the people involved should have sounded like rocket science until a few decades ago, but now, using the right technologies, tools, and workflow is affordable and hugely convenient. Managing all the necessary information in BIM (building information management) workflow, enables the involved actors to follow incoming data, collaborate, and exchange information related to the project through the entire project lifecycle.
Since we frequently work on international projects dealing with several actors in other countries, it is essential for us to share with the other designers all the information they need in a sort of 3D naked model. Ifc file, which scope is to interchange data or information without loss or distortion, plays a big role because of its international recognition and usage. Here is where and why a BIM software or any .ifc files viewer (we strongly suggest using the reliable BimVision) prove to be indispensable (we talk more about the digital model in this article on our website).
Details are also correlated with the industry standards of LOD or Levels of Development. The five-level development indicates the degree of reliability of the information and data included in the 3D model. By using LOD specifications the stakeholders can benefit from clear communication avoiding misunderstandings and errors.
Did you know we dedicated an entire technical article to LOD? To read more about this topic click on the image.
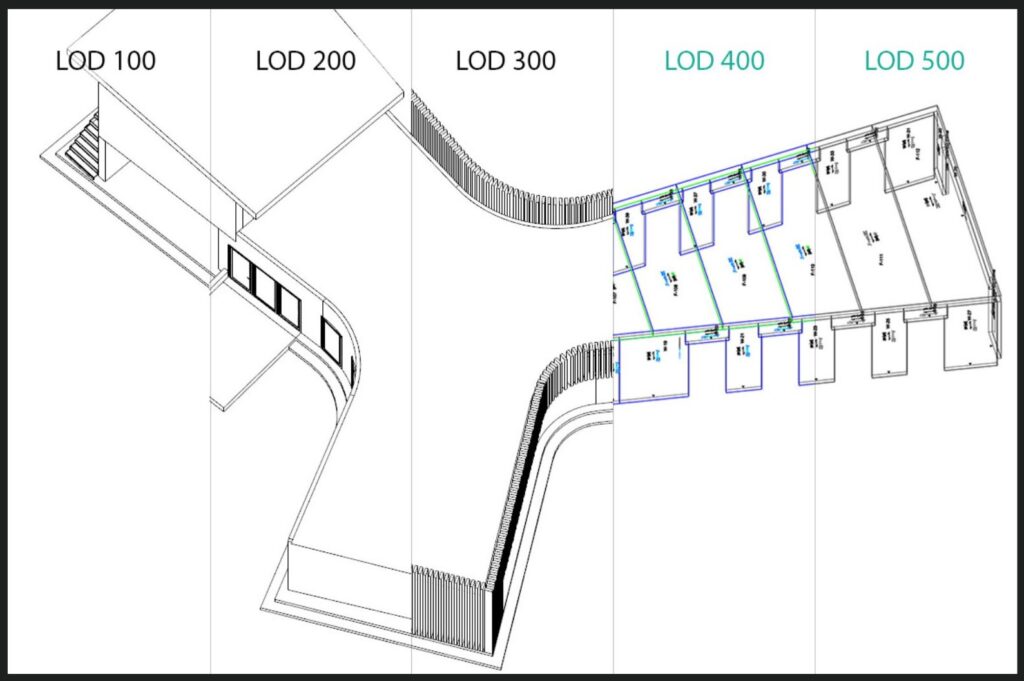
Moreover, in order to highlight the pivotal role of the littlest features and details, its necessary to comprehend that they need to be designed and studied from the structural point of view but also from the building’s physic one. A clear example of this is shown in our technical article where with the use of 3D Thermal FEM analysis, we verified there was no thermal bridge in the windows frame.
The more all kinds of details are available, visible, and understandable to all the stakeholders during the design process, the fewer inconsistencies, delays, and problems there will be during the construction stage. This will keep the project within the planned timeline and budget.