Detailing in mass timber engineering is not merely a task; it’s an art form that combines precision, technical skill, and deep understanding of the material and a wide experience. It’s not just using Cad software or implementing some macros in the workflow! The successful execution of timber projects depends on the engineer’s ability to work on every single detail (even the smallest one), ensuring structural integrity, safety, and longevity. We can undoubtedly include detailing into the super-skill kit a timber engineer must have to deal with Mass Timber Structures in the right way.
Unlike materials that offer a degree of forgiveness, timber demands a higher level of precision due to its natural variability.
As mentioned above, meticulous precision in detailing directly influences not only the structural integrity and durability of the final construction but also its aesthetic appeal and environmental impact, making detailed planning and execution a cornerstone of Mass Timber structures.
Timber detailing: differences with other building materials
Detailing in timber engineering significantly differs from the details required for construction using materials like steel or concrete.
For instance, while steel components can be connected through welding or bolting using standardized methods, designing timber connections is a highly time-consuming process. This process must consider various factors such as the forces involved, grain direction, moisture content, durability, long-term behavior, and geometric constraints. Therefore, in timber engineering, a holistic approach is essential, encompassing production, pre-assembly in the factory, transportation, and installation. At Ergodomus, we emphasize the importance of this holistic perspective; without a comprehensive understanding of the entire process, one cannot excel as a detailer.
Treating details with the importance they deserve is a skill not all engineers master correctly and efficiently. Knowing how to dedicate the necessary time, attention and resources to detailing is crucial in the production and processing of documentation critical to the project, for example:
- Digital IFC model
- Production drawings for timber elements
- Production drawings for steel elements
- Tollerances between different materials
Here below a Production Drawings’ slideshow useful to understand the level of detail that is achieved in producing these documents.
Sometimes we hear people say, ‘C’mon, it’s just drawings! Just hire some drafters and you’re all set.’ This couldn’t be further from the truth!
Detailing and Level of Development
Our work on project details follows the 80/20 rule, which we talk about in a special article. This principle means that getting from the start to 80% of the project (from LOD 100 to LOD 300) seems like a big part but actually only takes 20% of the time and effort.
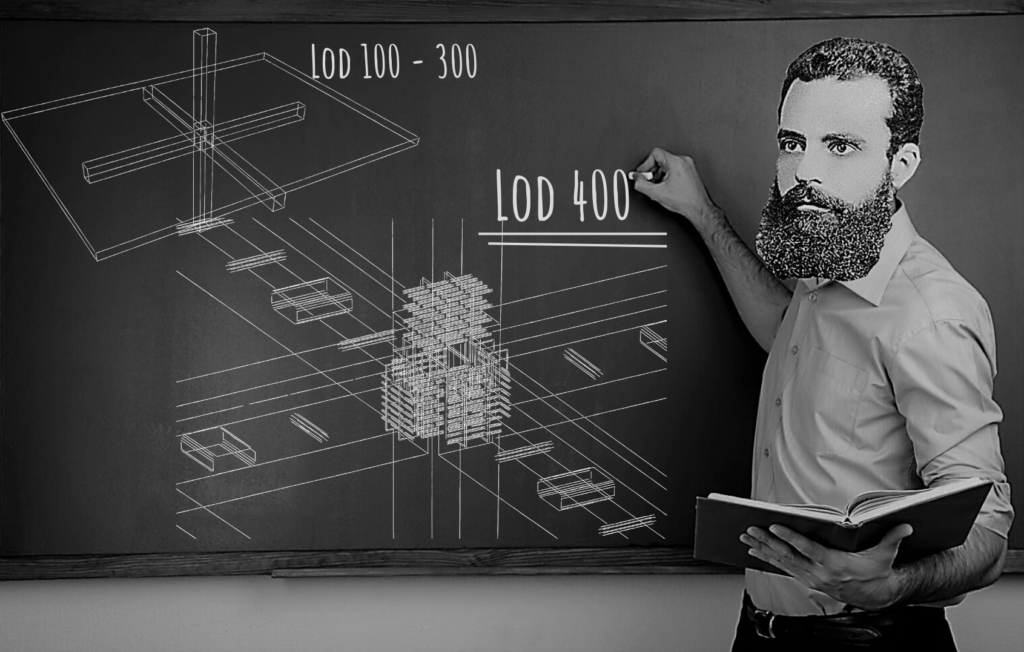
Pareto’s principle, which demonstrates that the relationship between inputs and outputs is never balanced, can be applied in many contexts. In most situations, including all Ergodomus’ projects, the 80/20 rule finds truthfulness; therefore, knowing where and when to dedicate most of our effort can save you a lot of energy and time.
Read the dedicated article by clicking the image!
The real work starts when moving from LOD 300 to LOD 400, the last 20% of the project. This part takes 80% of our time because it’s where we focus on the fine details, making very accurate CNC files, and formulating assembly and logistics plans. At this advanced stage, every model element is meticulously defined with production-specific information, ensuring all structural connections are precisely designed and any potential conflicts are resolved.
Based on our experience, we believe that if Pareto were a timber engineer, he would have modified the rule from 80/20 to 90/10, given the tremendous effort involved!
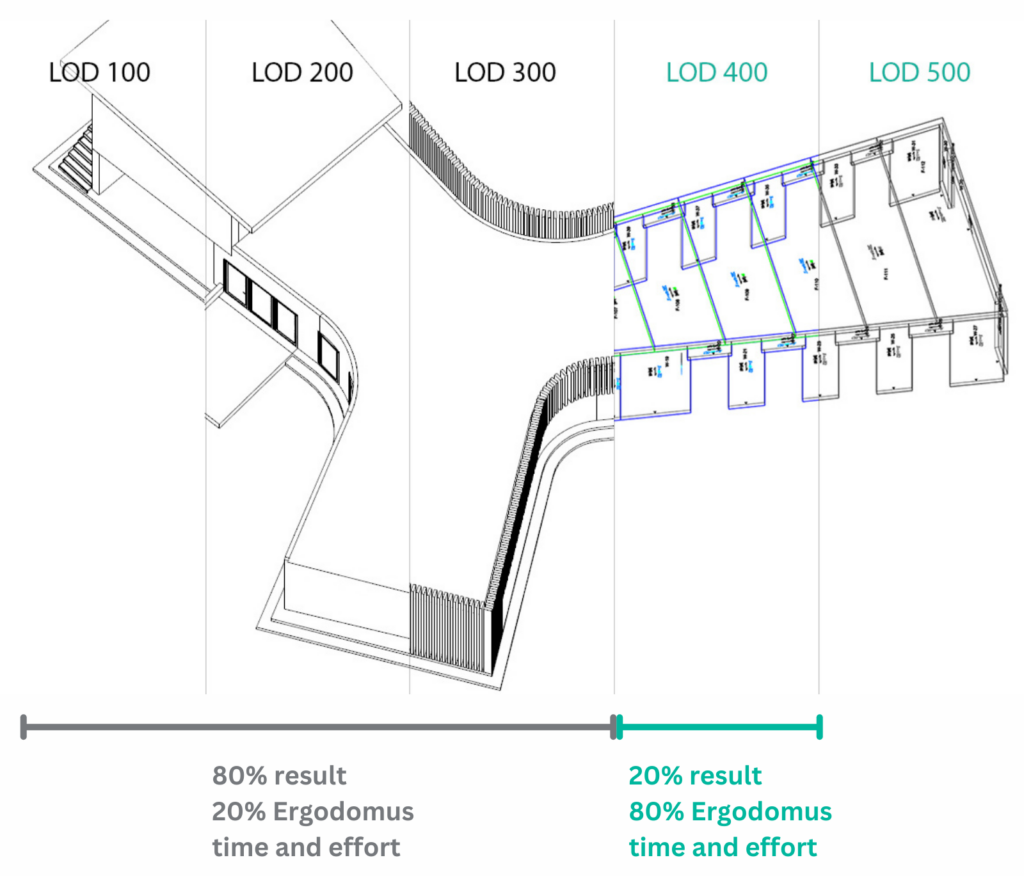
Although we have a great deal of experience in timber engineering, Mass Timber structures, and detailing each new project always presents unique and special challenges.
Projects and details
A valid example is the G124 project, an interesting structure we designed a few years ago for a public park. The structure could look like a “simple one” but in reality, since it is fully exposed to weathering all elements, both wood and steel, had to be designed and engineered with this factor in mind.
In fact, to enable the structure to withstand the weather and time, guaranteeing it a long life within the park, a number of specific details have been implemented.
Firstly, the connections between the beams and columns throughout the structure include a crucial detail visible in the images below. A gap of 15 mm was left between these two main types of elements to allow water flow and avoid dangerous stagnation.
Secondly, another important detail related to water and rot concerns the base of the columns. In addition to being raised off the ground to prevent the head of the columns from absorbing moisture from the soil, the support plate was recessed inward a few centimetres. This design ensures that water does not infiltrate between the GLT and the plate, allowing it to fall directly to the ground.
These thoughtful details collectively enhance the durability and longevity of the structure, ensuring it remains a resilient and lasting feature within the park.
Time is money
We all know that “time is money”. Assembling a timber structure is time-consuming, involving numerous people and specialized equipment. The cost equation is straightforward:

It’s evident that faster assembly leads to lower costs. Efficient detailing can significantly reduce both productive and unproductive time, which ideally should be minimal. In practice, however, unproductive time can account for more than 30% of the total assembly time!
There is a “hidden cost” to consider, which is the off-site cost. For example, a connection pre-assembled in the factory might reduce on-site productive time, but it increases off-site costs, which are generally quite low. Timber engineers need to be very familiar with the production process to account for these “hidden costs”, while also significantly reducing on-site time through expert engineering and detailed connection planning.
So, while the “off-site” cost represents an additional expense (+), it conversely leads to a reduction (-) in the assembly time on-site. Hence, the reduction in productive time can be influenced by several factors:
- The experience of the detailers/timber engineers
- A comprehensive understanding of:
- The entire process in a holistic manner
- The standard connectors available on the market
- The ability to create custom connectors
- The various methods for lifting and assembling the structural elements
- The logistics
- The time detailers/timber engineers invest in the project
The adage “You get what you pay for” resonates profoundly in timber engineering. It implies that to minimize time, risks, and problems on-site, one must consider this cost. Effective timber engineering demands not only financial investment but also a commitment to detail and quality.
In the next article
In our next article, we will dive deeper into the world of detailing throughout the entire design process, examining the intricacies of the IFC model, and exploring the nuances of production drawings for both timber and steel. Stay tuned for an in-depth analysis that will enhance your understanding of the pivotal role of detailing in timber engineering.