How long would it take to copy the bible by hand?
This could sound like a nonsense question since we’re talking about timber. Plus, why the bible?
Monastic scribes took hours and hours to copy it and other books by hand, letter by letter, drawing by drawing: it is estimated to approximately 600hours per book (theanalogpastor.com), 1,5-2 books per year for a person. As you can imagine, this limited a lot the diffusion of books and knowledge at that time.
Around 1450 the German Johann Gutenberg brought a disruptive revolution by creating the movable type: since then, everything has changed and he printed about 180 copies of the bible in 3-5 years. Perhaps it is not known that Gutenberg was not in the printing business as you might expect, he was trained in the metal work; so this disruptive revolution was brought to the market by someone from a different business.
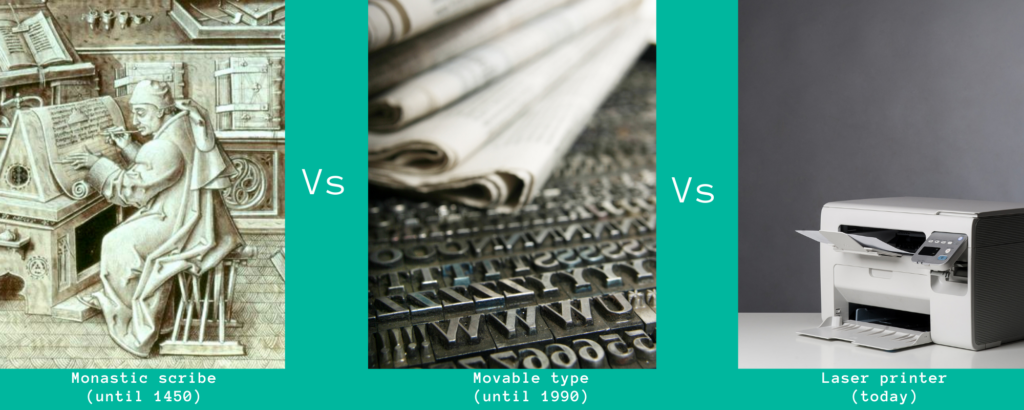
This technology has been improved for centuries but about 30 years ago something happened. In the ‘90s another revolution was born, this time not in Germany but in the Silicon Valley and was called DTP (Desktop Publishing): the digitization of the process with the motto “What You Draw Is What You Get” and no more movable type. In a few hours, thanks to a desktop computer and a laser printer, it was possible to create and print a newspaper, an invitation letter, a magazine, or a company flyer. Companies like Xerox and Quark changed the market again.
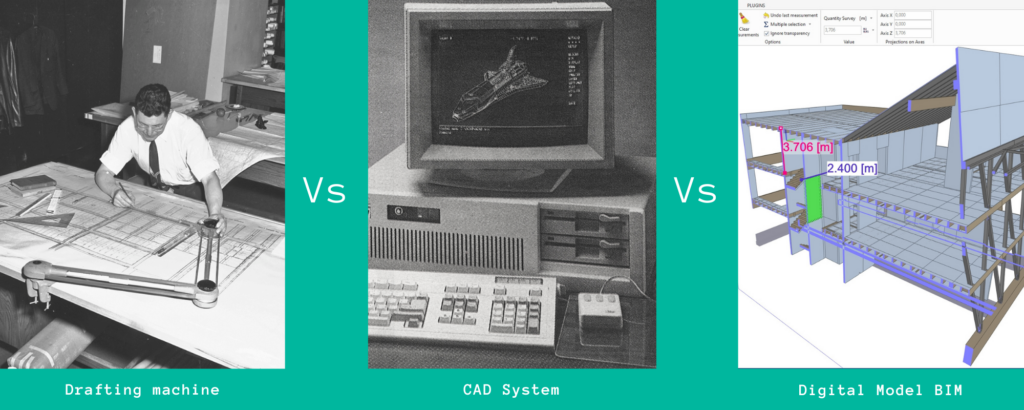
As designers, we experienced a similar (R)evolution: first the drafting machine with ink and transparencies (monastic scribe), then the CAD software (Gutenberg) and finally the 3d digital model – digital twin (DTP). Digitization had (and still has) a big impact on many different industries, but sadly the building industry seems to be very slow/skeptical in adopting/embracing new technologies.
Why? We’re not talking about super expensive computers and/or technologies that will be available in 5-10 years; we’re talking about the present, something you can buy in every computer shop today, right after you finish reading this article.
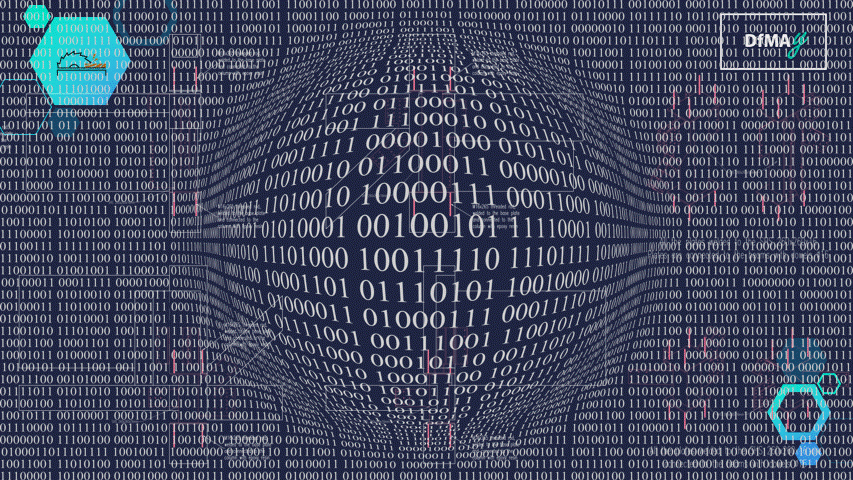
Digital models can be very easily shared among the designers and the customers; they can be used to get much information like quantities, carbon impact, costs, logistic aspects, maintenance, etc… We even created augmented reality APPs on both the Android and Hololens platforms (see the articles at the bottom).
All this can be easily achieved while working remotely. What still amazes us, is that you can quickly compare dozens of different solutions to each other and find either the most cost-effective one, or the cheapest one or the most sustainable one. We, as timber engineers, have been using the digital model for years, without even knowing its “real name”. Every project we work on is fully digitized, and every single element we draw has some specific properties: length, width, depth, density, cost per unit, CO2 stored per unit, assembly number, mechanical grade, truck ID, container ID, etc… Therefore, the .ifc model we share with the other designers has all the information they need; it’s like having a naked 3d model. As you can see in the images below, by clicking on a solid element you can see all its properties: you just need a BIM software or an .ifc viewer (there are many of them totally free and we strongly suggest BimVision).
Examples of how the .ifc file can be opened and analyzed on both Revit and BimVision.
For a timber engineer, the digital model must be more than perfect and the reason is very simple: we get the CNC files from the digital model. This means that if something wrong is drawn, the CNC machine will produce the wrong element and there will be problems on site.
The workflow and the basic principles are very similar to the 3d-printing technology since now the hardest part is not the production anymore, it is creating the perfect 3d model instead, then a machine will create the item from scratch, no matter how complex it is and how long it will take.
A part of a project 3d-printed with double curved and twisted glulam beams.
We truly believe it is time to change the way we design buildings by embracing new technologies. Not just because it is “in fashion”, but because they allow us to value the project and to reduce the time during both the engineering process, especially, on-site.
We can’t stay with the “movable type” anymore!