When Architects, Engineers, and Fabricators Collaborate
The Urgent Need for a Faster, Smarter Building Method
Housing shortages are at an all-time high, pushing developers to seek faster, more cost-effective construction methods. Choosing the right construction method (MMC) is very important for developers. Off-site manufacturing can dramatically reduce on-site labor and speed up assembly, but it’s no simple “plug-and-play” solution.
Since 2007, we at Ergodomus have seen many companies promise quick builds but struggle with real-world complexities—regulatory approvals, supply chain snags, shipping logistics, and more. The “crane-lifts-three-modules-an-hour” moment may look magical on social media, but it’s only possible through meticulous, holistic planning and execution behind the scenes.
What Is VTMB (Volumetric Timber Modular Buildings)?
We’ve coined the acronym VTMB, which stands for Volumetric Timber Modular Buildings. Essentially, entire volumetric units—complete with walls, floors, finishes, and MEP—are produced off-site from engineered timber. These units are then transported and rapidly assembled on-site, forming anything from single-story to multi-story dwellings, educational facilities, healthcare projects, and commercial buildings.
Our VTMB approach isn’t theoretical: we’ve used it on real projects, refining our methods through hands-on experience. Each lesson learned is integrated into our designs, ensuring the modules are safe, efficient, and structurally sound throughout their lifespan.
Standardized Solutions Don’t Mean Inflexibility
Standardization in modular construction doesn’t mean a lack of flexibility. Design for Manufacture and Assembly (DfMA) keeps a core framework consistent while allowing finishes, layouts, and aesthetics customisation. This approach reduces redundant re-engineering, making the process smoother and more efficient.
Well-developed modular technology includes a comprehensive building kit with essential engineering details for building structure, MEP, HVAC, and electrical systems, along with integrated solutions for structural integrity, fire safety, acoustics, and thermal efficiency. These built-in standards ensure each module meets high-performance criteria from the start.
Every project needs customization to address geography, building codes, and market preferences. The key is to balance standardized efficiency with the flexibility needed for each unique build.
A Holistic Approach: The Pillars of VTMB Success
Delivering successful VTMB projects requires coordinating each of the following elements from day one, ensuring they fit seamlessly together.
Structural Analysis & Robustness
Timber offers an excellent strength-to-weight ratio, but precise engineering ensures the modules meet performance requirements, especially for multi-story buildings.
Robustness is crucial: if one module were to fail (due to extreme damage or a localized event), the design must prevent a domino effect of progressive collapse. Our dedicated article covers more about robustness.
Fire rating also ranks high among design priorities. Timber can be engineered to meet stringent fire codes, often through smart detailing, charring design, and the inclusion of protective layers (e.g., gypsum board). Coordinating these details early on ensures compliance without last-minute surprises.
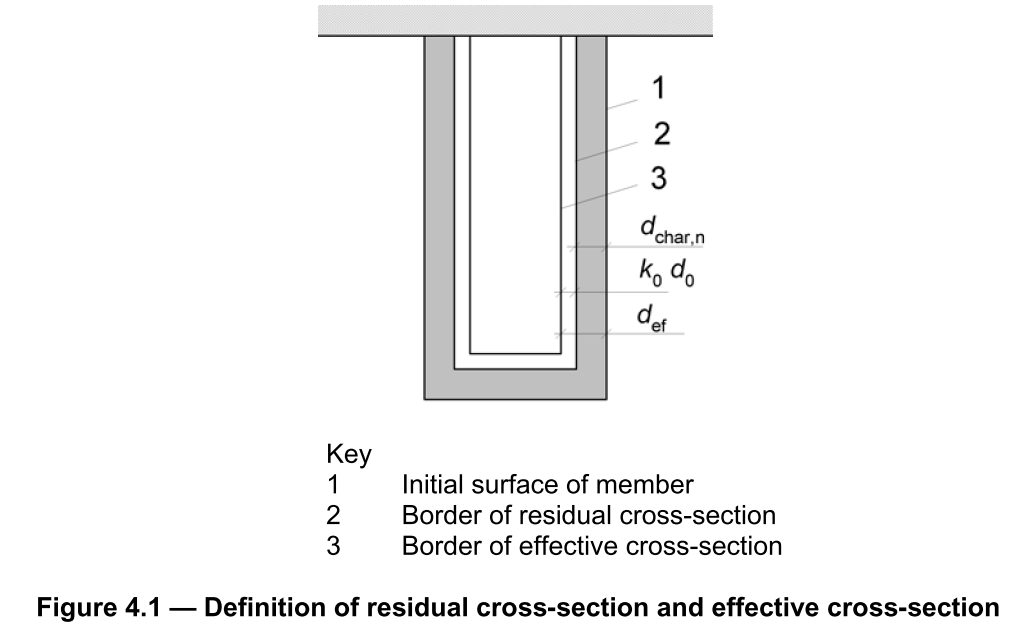
Building Physics
Managing moisture and humidity can make or break a timber building’s longevity. Overlooked leaks or condensation can lead to hidden structural issues down the road.
Wet areas like bathrooms or kitchens require special attention to waterproofing and vapor barriers.
Acoustics must be carefully planned; the assembly’s layering (insulation, resilient channels, etc.) helps reduce sound transmission between modules.
Complex Production Drawings & DfMA
Off-site construction demands rigorous alignment between design intent and factory capabilities.
Connection design is especially critical in volumetric modules: simple, repeatable connections guarantee quick and perfect vertical/horizontal alignment. This way, on-site teams don’t waste time measuring and adjusting each module.
Detailed production drawings must reflect exactly how modules are fabricated, handled, and assembled. A small oversight in a 2D drawing can become a major delay on the factory floor.
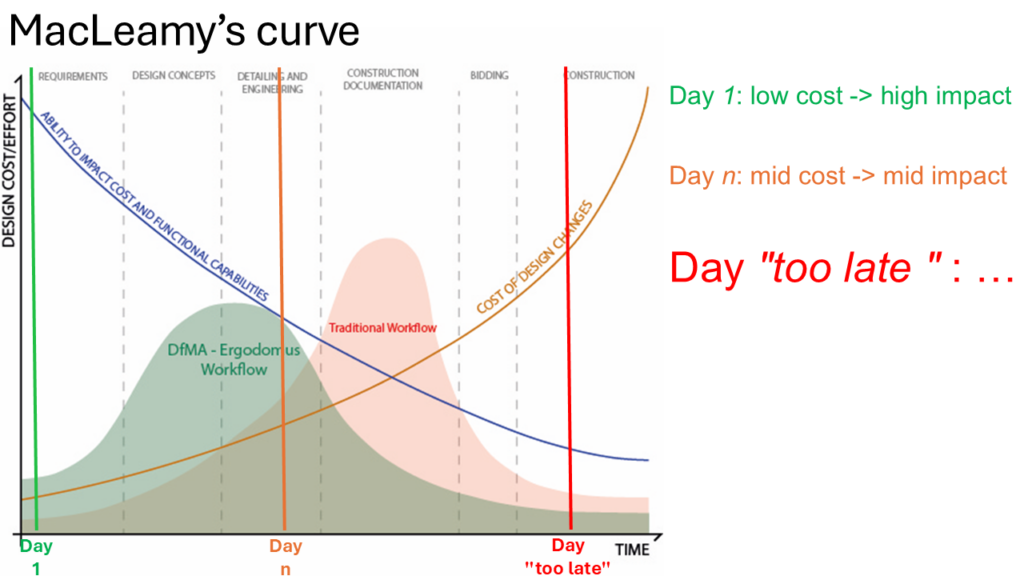
Logistics & Supply Chain Management
Modules may be moved by truck, train, or boat—each mode imposes its own constraints on dimensions, weight, and protective packaging.
If a key supplier delays even a single component, the entire assembly line can stall. Therefore, a Plan B for materials is essential.
The last-mile delivery to the job site also needs careful planning—tight urban sites or narrow roads can complicate module positioning and crane operations.
Cost Analysis & Production Limitations
Off-site manufacturing can save on labor and reduce waste, but every detail—from material selection to transportation route—impacts cost.
Factories have throughput limitations. One breakdown in equipment or workforce shortage can ripple across project timelines. A well-managed schedule is critical for success.
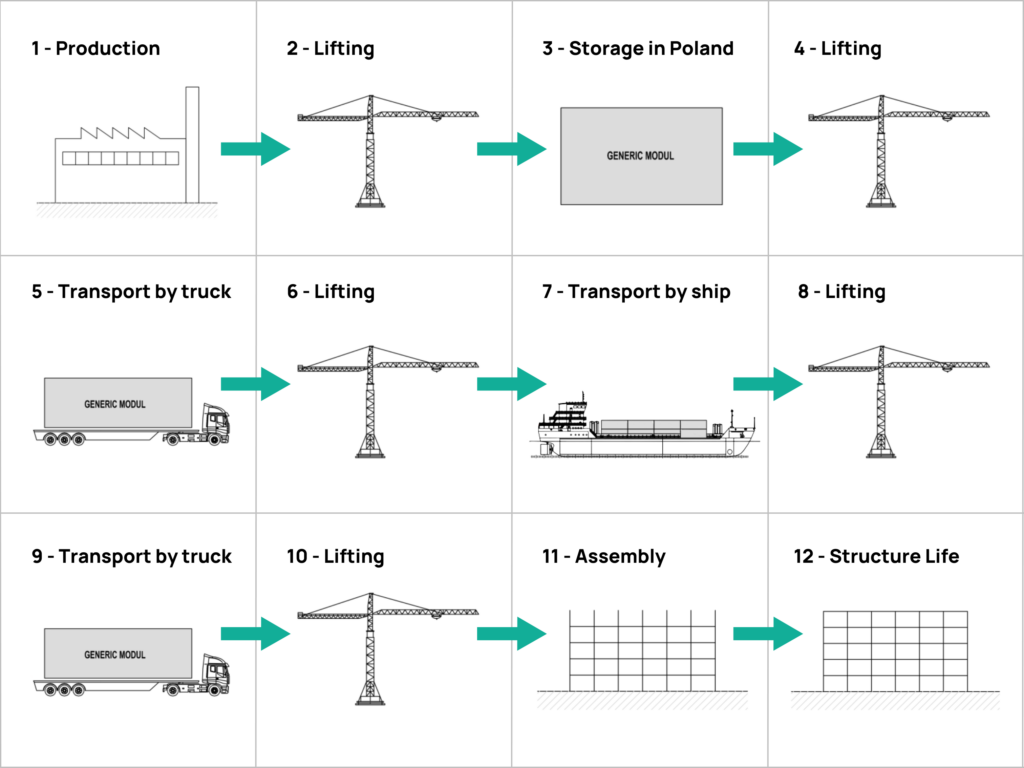
Project Management from Day One
True modular success arises from end-to-end coordination. A project manager (or integrated team) must monitor structural engineering, production scheduling, logistics, and on-site assembly closely.
DfMA thinking requires everything to be mapped out well before the first nail is driven in the factory. Even minor design changes can trigger major cascade effects if not communicated properly.
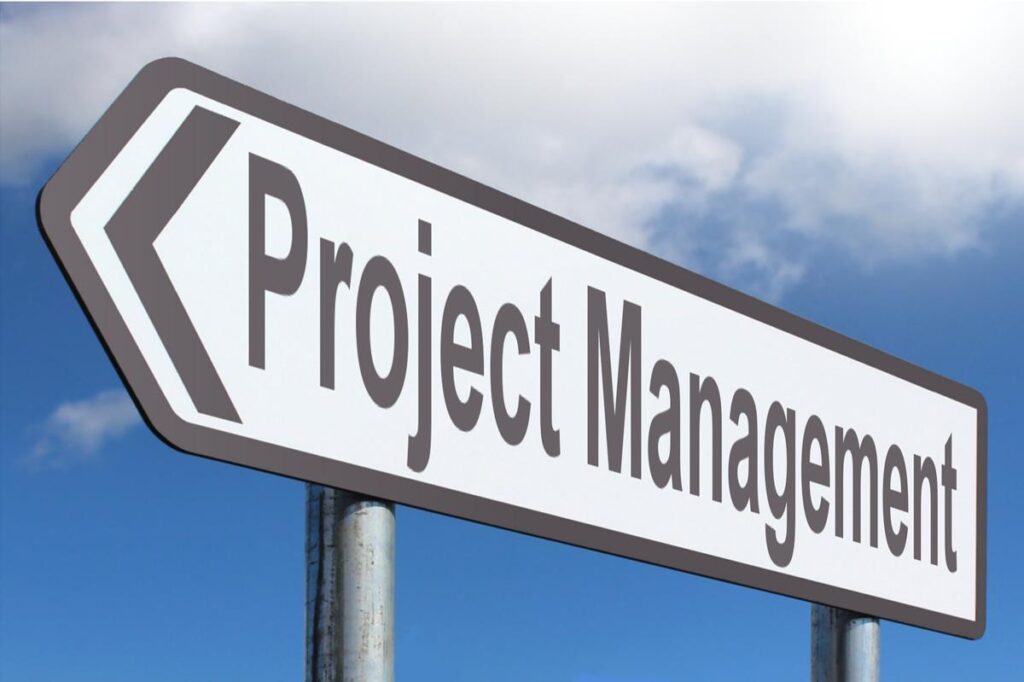
Collaboration: Architects, Engineers, and Fabricators
All the pillars above converge on four key players:
- Architects – Masterminds of the building’s function and aesthetics. They shape space, form, and user experience but must align design choices with modular constraints.
- Engineers – Ensure structural integrity, optimize building physics, and guarantee code compliance, including fire safety and robustness.
- Fabricators – The experts who turn digital designs into tangible modules, ensuring each connection is precisely built for efficient on-site assembly.
- Assembly Teams – Ensure successful assembly of modules precisely according to technology and in a short time.
If any one of these teams operates in a silo, the entire project risks cost overruns, delays, or fundamental design conflicts. Early, continuous collaboration is non-negotiable for VTMB success.
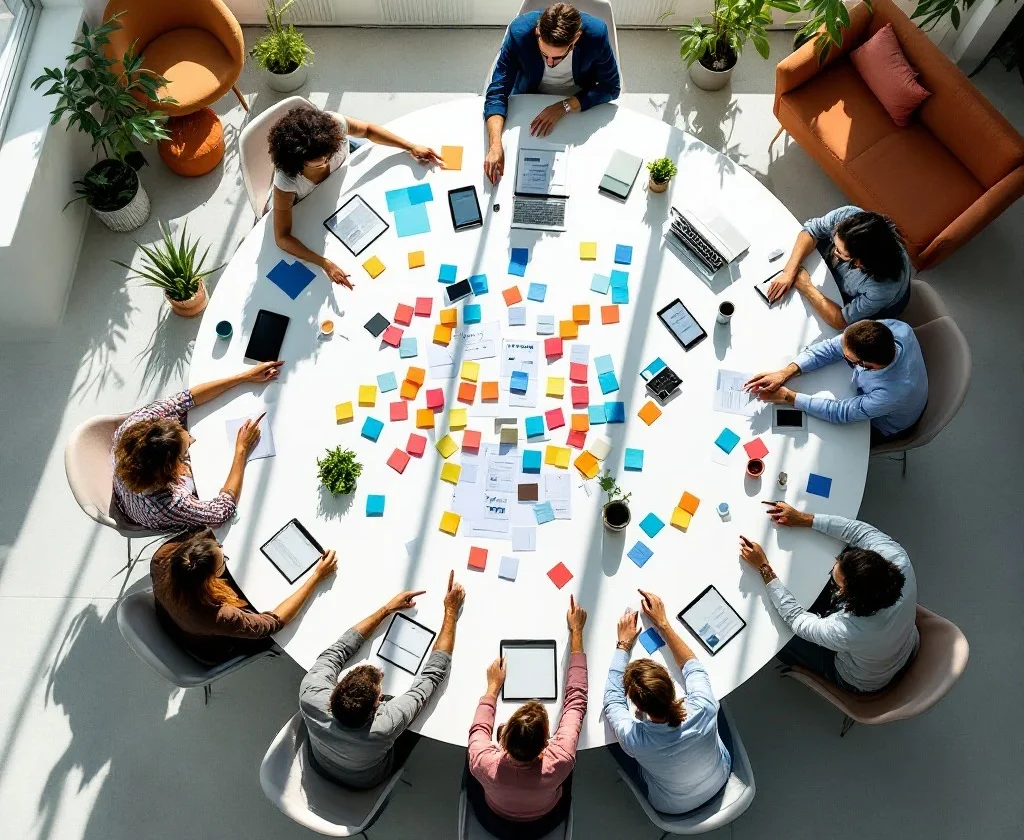
Real-World Results, Not Just Theory
We’ve been delivering engineered timber solutions globally since 2007, seeing firsthand how “little things” (like detailing connections or planning transport routes) can spell the difference between a smooth project and a logistical nightmare. Our VTMB approach evolved from these experiences—learning from challenges, integrating best practices, and continually refining our method.
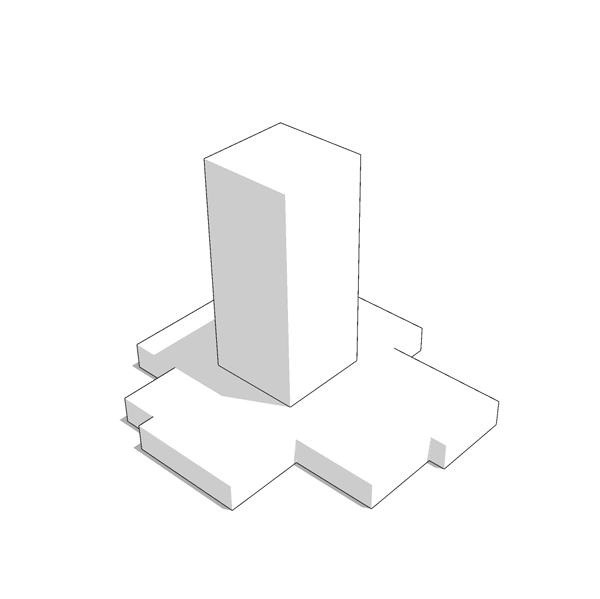
Let’s Hear Your Thoughts
Now we want to hear from you!
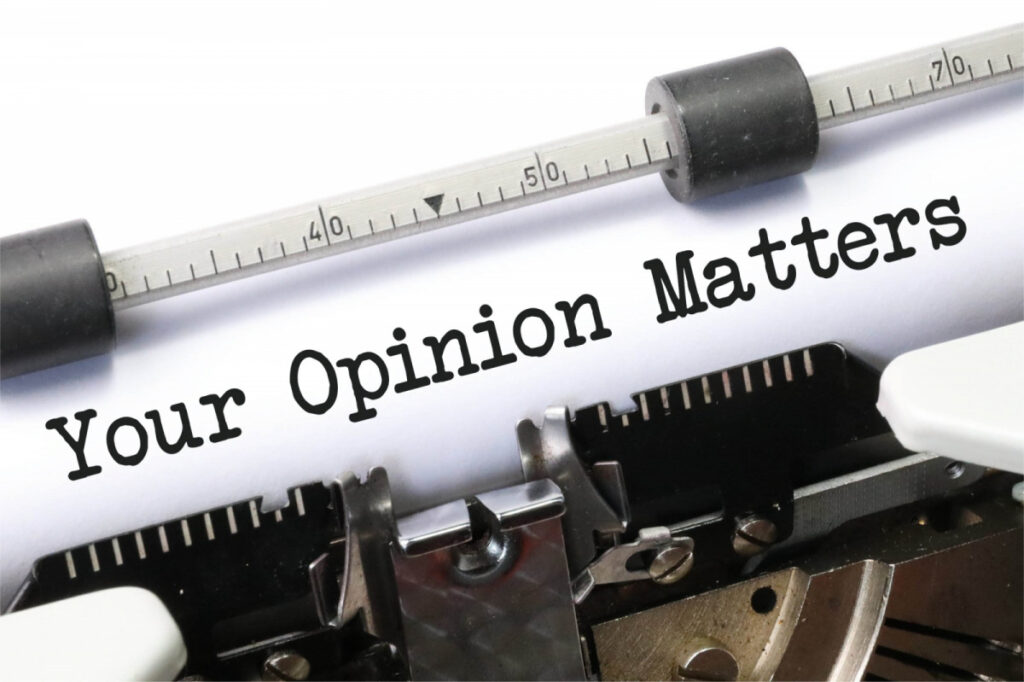
- Which aspect of VTMB do you think poses the biggest challenge? Fire safety? Managing wet areas? Logistics between factories and job sites? Something else entirely?
- Have you already tried volumetric modular construction? If so, what motivated your choice—and would you choose it again? Or have you decided against it, and why?
- What have been the biggest pros and cons in your experience? Did the speed and potential cost savings offset any logistical hurdles or design limitations?
- Did you face any unexpected hurdles along the way? We’d love to learn from your story whether it was connection design, supplier delays, or code compliance issues.
- If you haven’t tried it yet, what’s holding you back? Is it cost uncertainty, lack of familiarity, or something else?
- Do you believe VTMB can significantly help tackle the housing crisis—or is it more of a niche approach?
- What role, if any, should governments play in encouraging or regulating modular solutions? Could policy support be crucial for scaling up?
- Could VTMB also be effective in underserved or developing regions, where speed and cost are critical? Or do you see obstacles that might limit its viability?
Drop a comment on LinkedIn here or share this article with a colleague who’s exploring modular buildings. Let’s start an open dialogue—both the upsides and the downsides—on how VTMB can address the urgency for faster construction while meeting the realities of engineering, fire protection, and code compliance.
Final Thoughts & Next Steps
Stay tuned for future articles where we’ll dive deeper into the common pitfalls of volumetric construction, why standardized solutions don’t have to limit creativity, and the ongoing R&D efforts that keep VTMB evolving. In the meantime, join the conversation in the comments below—we’d love to learn from your experiences in off-site construction!